L’industrie du futur : repenser les relations clients-fournisseurs
Beaucoup d’entreprises ont entamé une réflexion au plus haut niveau sur leur positionnement futur, incités en cela par les nombreuses initiatives soutenues par les gouvernements : Industrie 4.0 en Allemagne, Usine du futur en France, Smart Manufacturing aux Etats Unis, …
Les réflexions sont menées avec l’objectif de repenser les relations clients-fournisseurs de manière à pérenniser et re-dynamiser les activités des entreprises dans un contexte de mondialisation ultra-compétitif. La crise sanitaire COVID-19 récente n’a fait qu’accentuer le phénomène. Il est aussi question d’utiliser au maximum les technologies digitales qui sont indispensables à la mise en place de ces nouveaux concepts.
Les réponses apportées par ceux qui ont abouti dans leur démarche se traduisent notamment par la transformation du marché. L’entreprise passe de la vente d’un produit à la vente d’un service.
Michelin qui vend des kilomètres parcourus ou un nombre d’atterrissages est un exemple souvent cité de cette transformation de la relation client-fournisseur.
Cela peut aussi se traduire par une capacité de re-localisation des activités de production.
Enjeux pour la production : standardisée mais agile à la fois
Le changement de la relation entre les clients et les fournisseurs a évidemment un impact direct sur les ateliers de production. Dans tous les cas, la transformation de l’entreprise sera une réussite uniquement si la production est suffisamment agile. Autrement dit : elle est capable de faire des séries plus petites, de personnaliser les produits de masse, tout en gardant des coûts de production compétitifs.
La solution passe donc par la révision du fonctionnement de l’entreprise, accompagnée d’une forte standardisation des processus de production et des indicateurs de performance qui auront été définis en adéquation avec la stratégie de l’entreprise.
L’utilisation de la norme ISA-95 en support de l’exercice de modélisation/standardisation des activités de l’entreprise y trouve plus que jamais tout son sens !
Le MES (Manufacturing Execution System) au cœur du système d’information (SI) ?
La traduction sur le terrain des processus repensés passe nécessairement par leur digitalisation et par une révision de l’architecture des systèmes d’information. Le logiciel MES a une place centrale dans l’architecture dans la mesure où il est l’élément orchestrateur de la production, en soutien aux opérateurs. La mise en place d’un logiciel MES, épaulé par des technologies nouvelles telles que l’IIOT (connectivité), la réalité augmentée (Interface homme-machine), l’IA (intelligence artificielle), ouvre la porte à un pilotage pro-actif des ateliers. Le logiciel MES n’est alors plus uniquement un outil de construction de rapports. Il donne de la visibilité en temps réel sur ce que sera le futur à court terme en mettant en évidence des aléas prédictibles et en donnant à l’humain le temps de la réflexion pour prendre la meilleure décision, à partir d’un environnement unifié.
Dans ce contexte, le logiciel MES est l’élément principal qui va permettre la transformation des relations clients-fournisseurs. Il en devient un élément indispensable à la conduite des activités de production, au même titre que les automates programmables !
Conclusion : Le MES, 1er pas vers la transformation digitale des usines
La démarche présentée ici est souvent indispensable à la survie de l’entreprise. La traiter dans le bon ordre est la clé du succès.
Même si les logiciels MES sont aujourd’hui matures et prêts à supporter rapidement les processus flexibles, la transformation digitale de l’entreprise est un processus qui demande du temps (minimum 2 ans avec la réflexion préliminaire) et la mobilisation de tous les départements de l’entreprise !
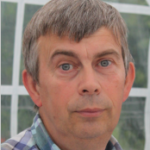
Cet article vous a plu ? Partagez-le sur Linkedin :