TRS, LIMS, SPC, APS, GMAO … à chaque département son outil, à chacun ses prérogatives et à chacun son information non partagée, ressaisie, partielle, à posteriori …
Le MES / MOM permet de couvrir l’ensemble des processus de faciliter la communication autour d’une donnée unique, contextualisée et partagée et favorise l’automatisation de processus au sein des différents départements pour assurer une meilleur performance opérationnelle.
UN MONDE DE SILOS
L’ensemble des processus qui supportent la production sont interconnectés, on planifie les OF en fonction des maintenances prévues, on déclenche des contrôles qualité au démarrage d’un OF, on approvisionne en stock, on utilise des outils qui doivent être révisés…
Au quotidien les départements échangent des informations, des emails des appels et la performance dépend du bon rouage de ces processus oraux.
Chaque département possède son outil et améliore ses processus sans intégrer les autres départements à leur conception ou à leur communication… En conclusion l’information est disponibles dans ces nombreux applicatifs, une information non partagée qui empêche l’automatisation des processus
COLLABORER ET PARTAGER L’INFORMATION
Le rôle du MES trop longtemps cantonné à la mesure du TRS se déploie maintenant de façon complète dans les ateliers de production. Ces projets de transformation ne sont plus uniquement initiés par la production mais bien par l’ensemble des acteurs de la chaine de valeur de l’entreprise.
Au même titre que la gestion de l’entreprise repose sur un outil commun, l’ERP, la gestion des entités de production se calque sur ce modèle permettant une réelle collaboration.
Une collaboration sur la base des données. Elles sont identiques, elles sont temps réel, elles sont contextualisées… ce qui permet à chaque département de les utiliser au mieux dans leur
responsabilités quotidiennes mais ce qui permet aussi aux départements transverses de mener des analyses complètes sur l’ensemble des données (Production, Qualité, Inventaire, Maintenance…)
AUTOMATISER DES PROCESSUS
Une fois la donnée partagée, la prochaine étape est d’aller plus loin et de câbler des processus déclenchés de façon automatique.
A titre d’exemple, un paramètre de température monitoré sous SPC sort d’un comportement normal, une DI (demande d’intervention) est créée, la maintenance effectue une surveillance et décide d’arrêter la ligne en fin d’OF, un arrêt est généré automatiquement et le planning est averti en temps réel par message et email. La ligne redémarre, l’arrêt est immédiatement terminé, le planning a changé la séquence des OF, la logistique en a été informée et a apporté en pied de ligne le nouveau stock…
Des scenarios comme celui-ci vous pouvez en décliner à foison car l’ensemble des informations est accessible à un seul endroit. Au même titre que toutes les données de gestion sont au même endroit dans l’ERP. Feriez-vous machine arrière au niveau ERP ?
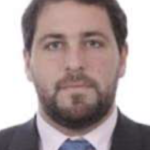
Cet article vous a plu ? Partagez-le sur Linkedin :